TECHNICAL LIBRARY
Rolled Alloys Metallurgical Services
Rolled Alloys offers global metallurgical assistance. With full metallurgical labs, we offer alloy corrosion testing and high temperature oxidation studies. After 70 years of experience in the heat treat industry the metallurgists have performed dozens of long term high temperature oxidation studies. With a global emphasis on corrosion resistant alloys and duplex stainless steels, we have performed various corrosion studies on iso-corrosion curves in acids, critical pitting, crevice corrosion and stress corrosion cracking tests. Additional laboratory services include multiple optical microscopes and SEM equipment. Rolled Alloys can help you find the best alloy suited for your application
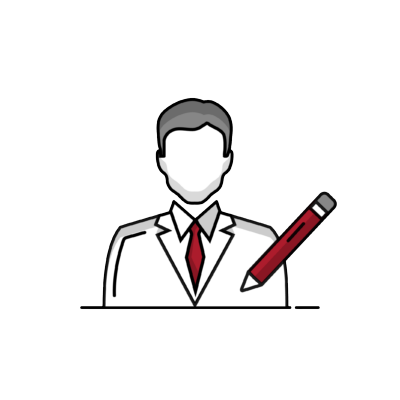
Ask the Metallurgical Services Team
Metallurgical Services is here to provide answers to your technical questions.
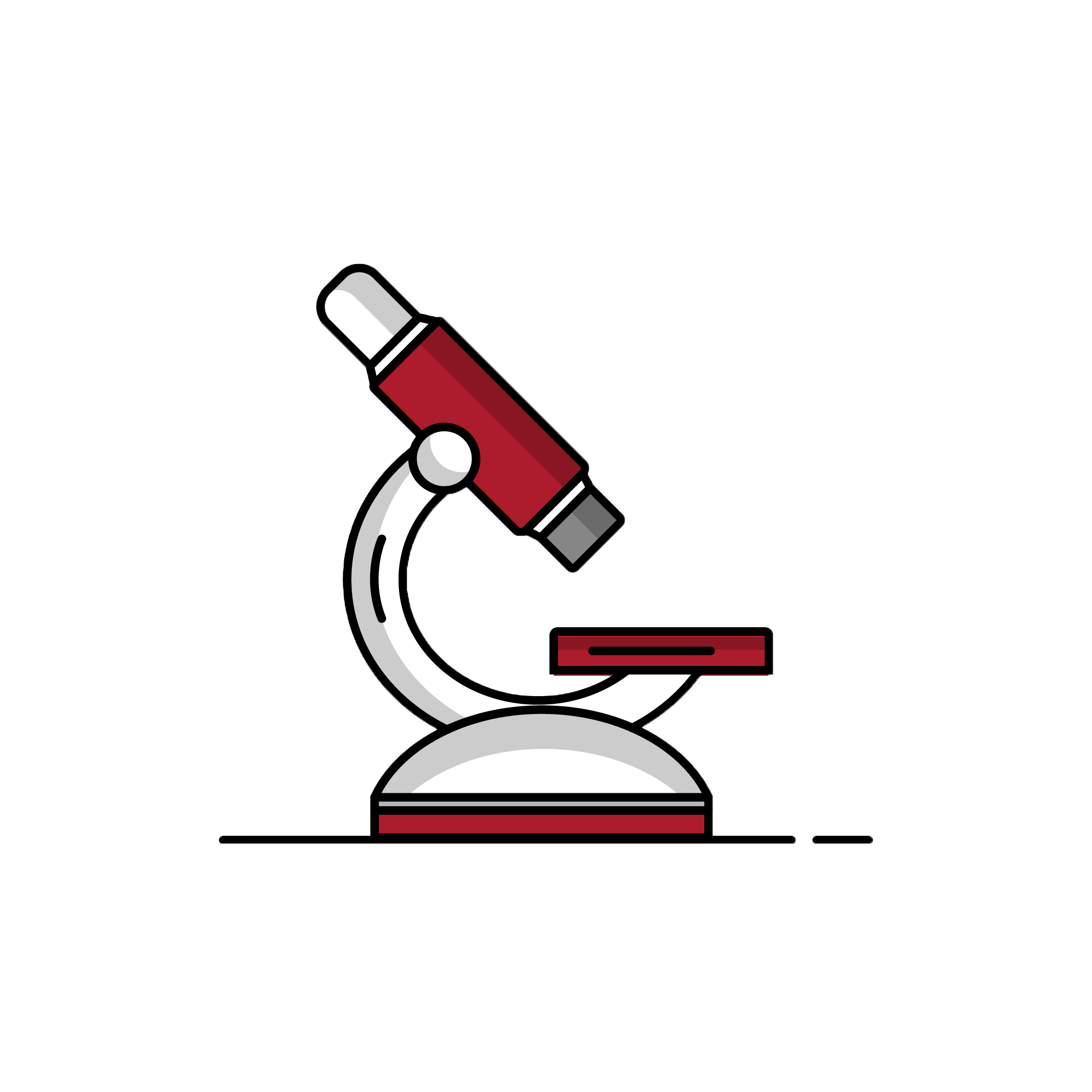
ID, Analysis, & Lab Testing
Our Metallurgical Services Team can help with the material selection process, and provide PMI.
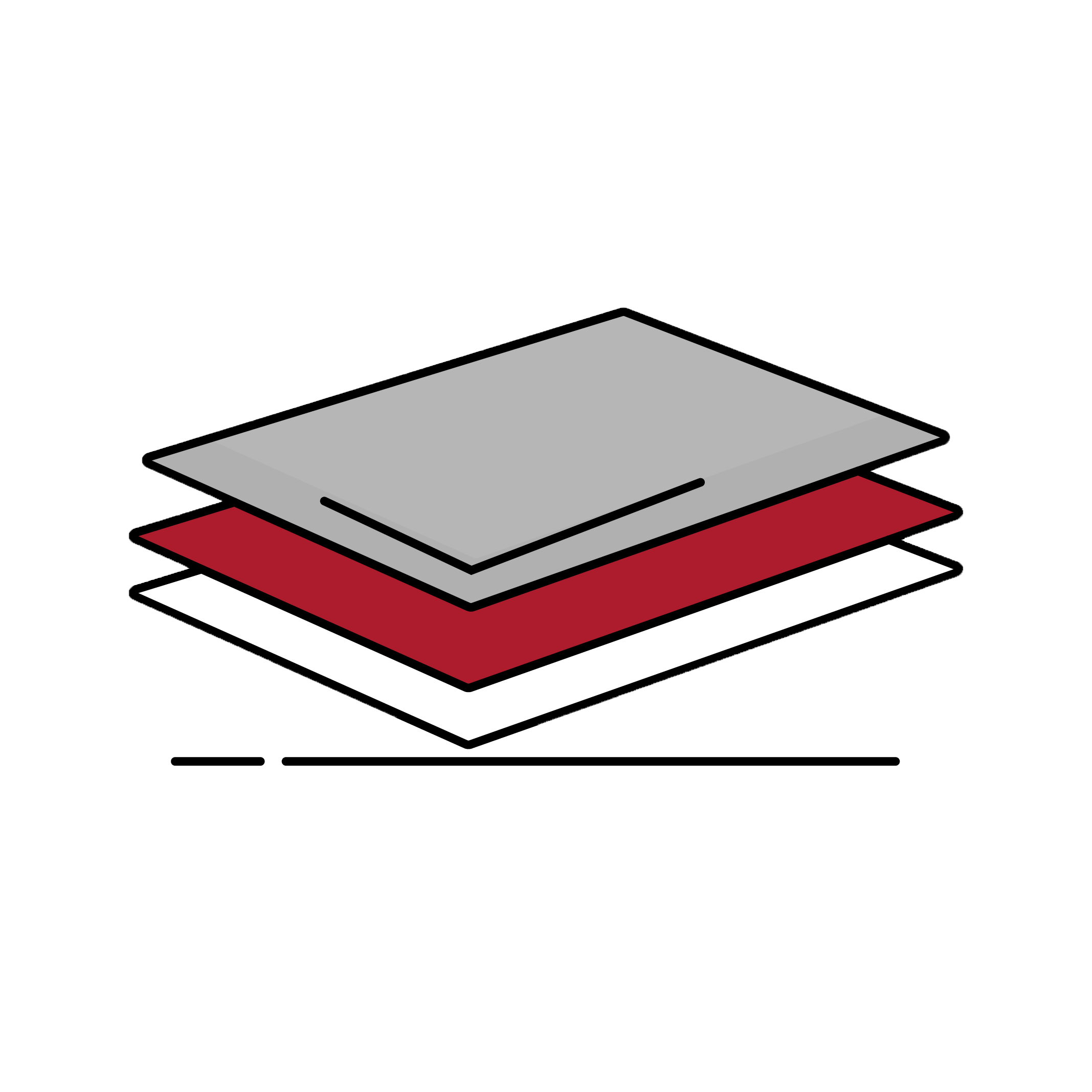
Sample Material
As part of our lab services, we provide sample coupons of various thicknesses.
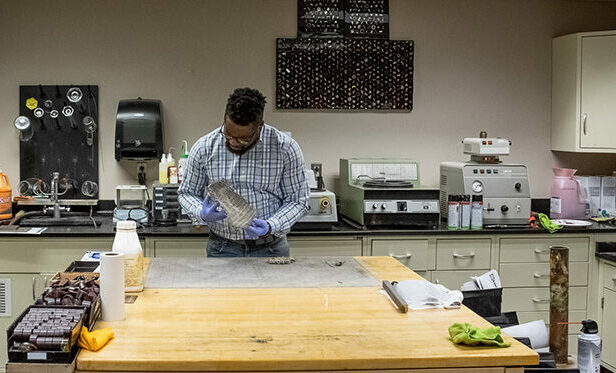
Fabrication Information
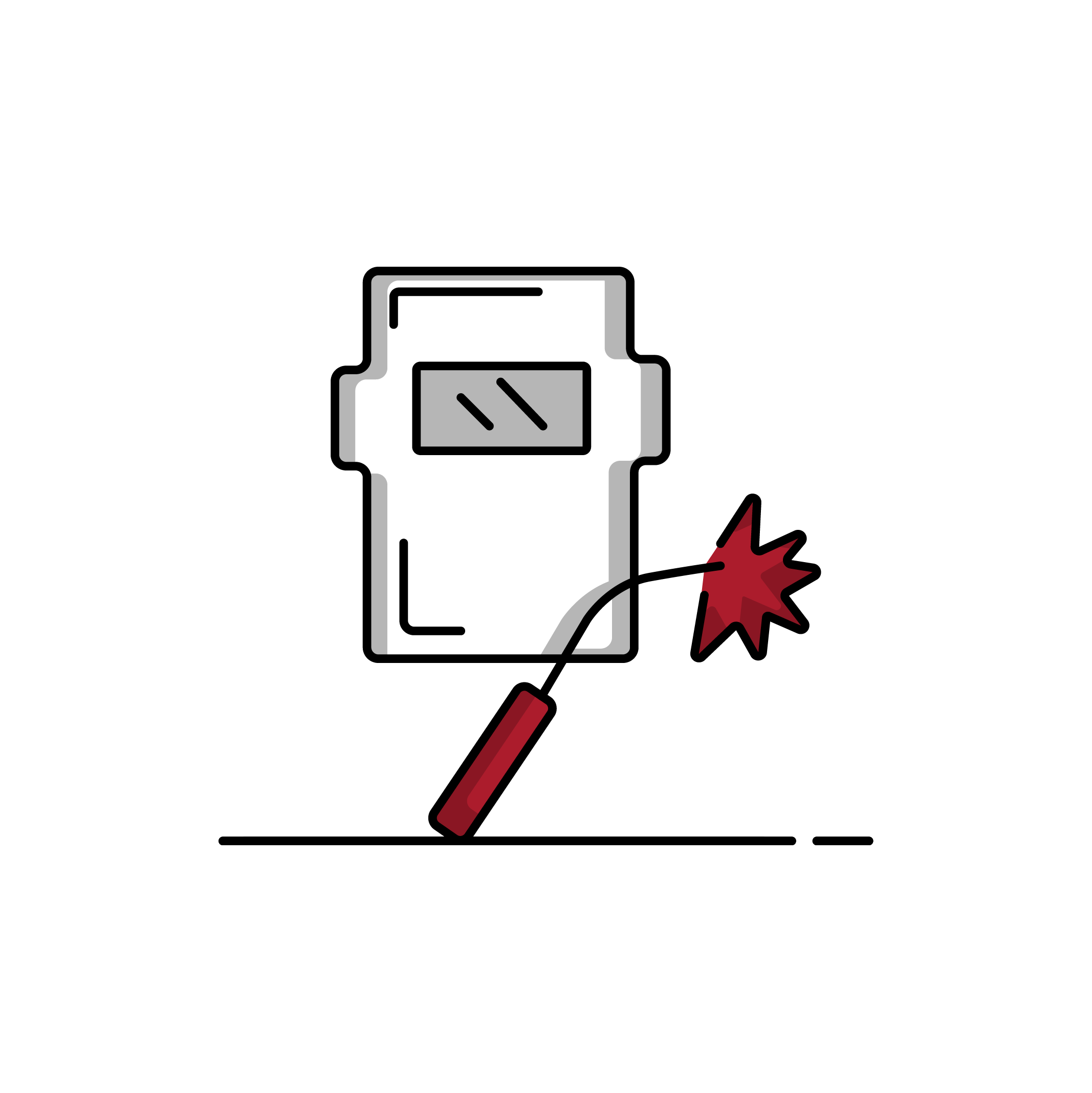
Welding
Looking for weld wire? Need to know how to weld your alloy? Check out the welding section for more information.
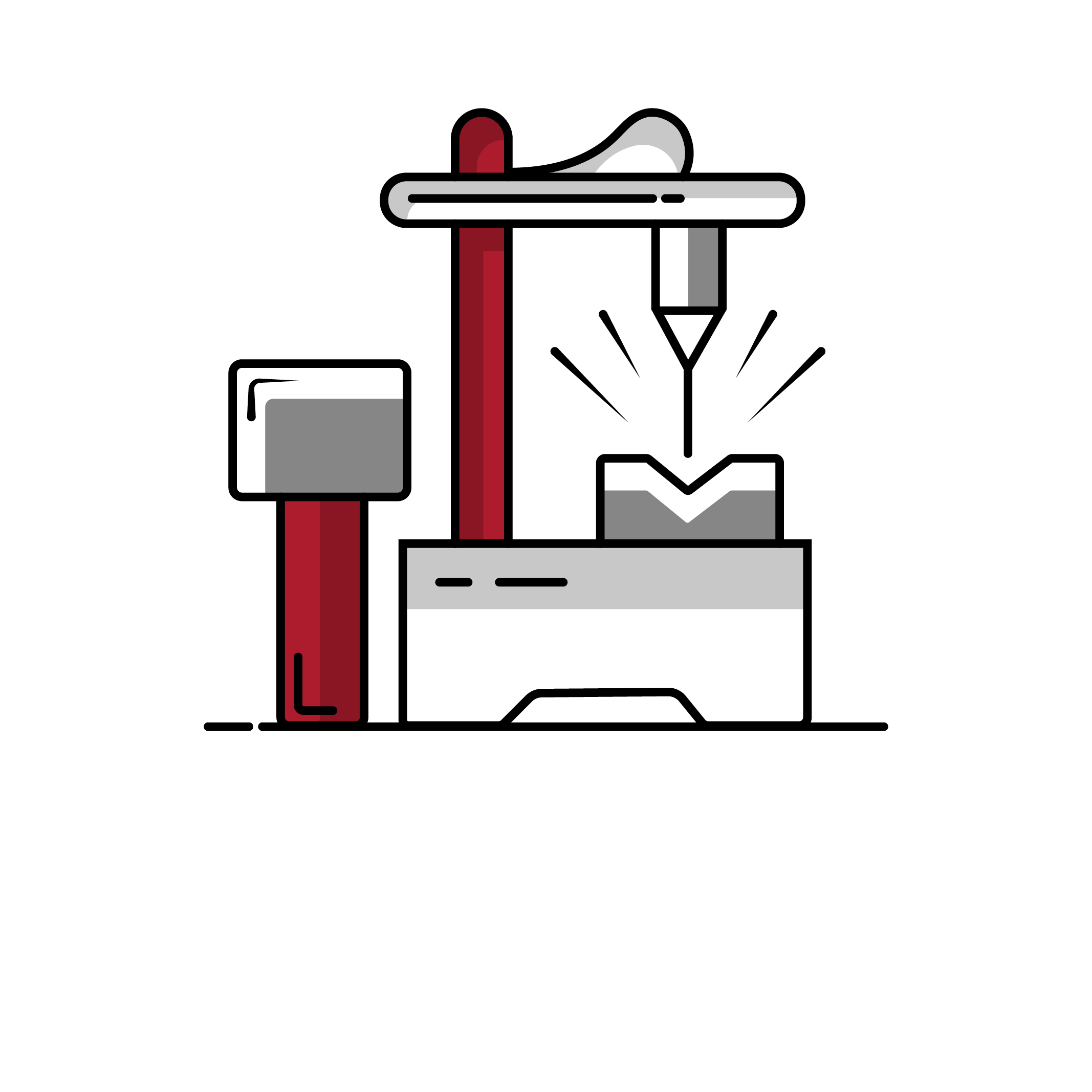
Forming
Need information on tensile forming, bending or shearing in regards to our alloys during plastic deformation?
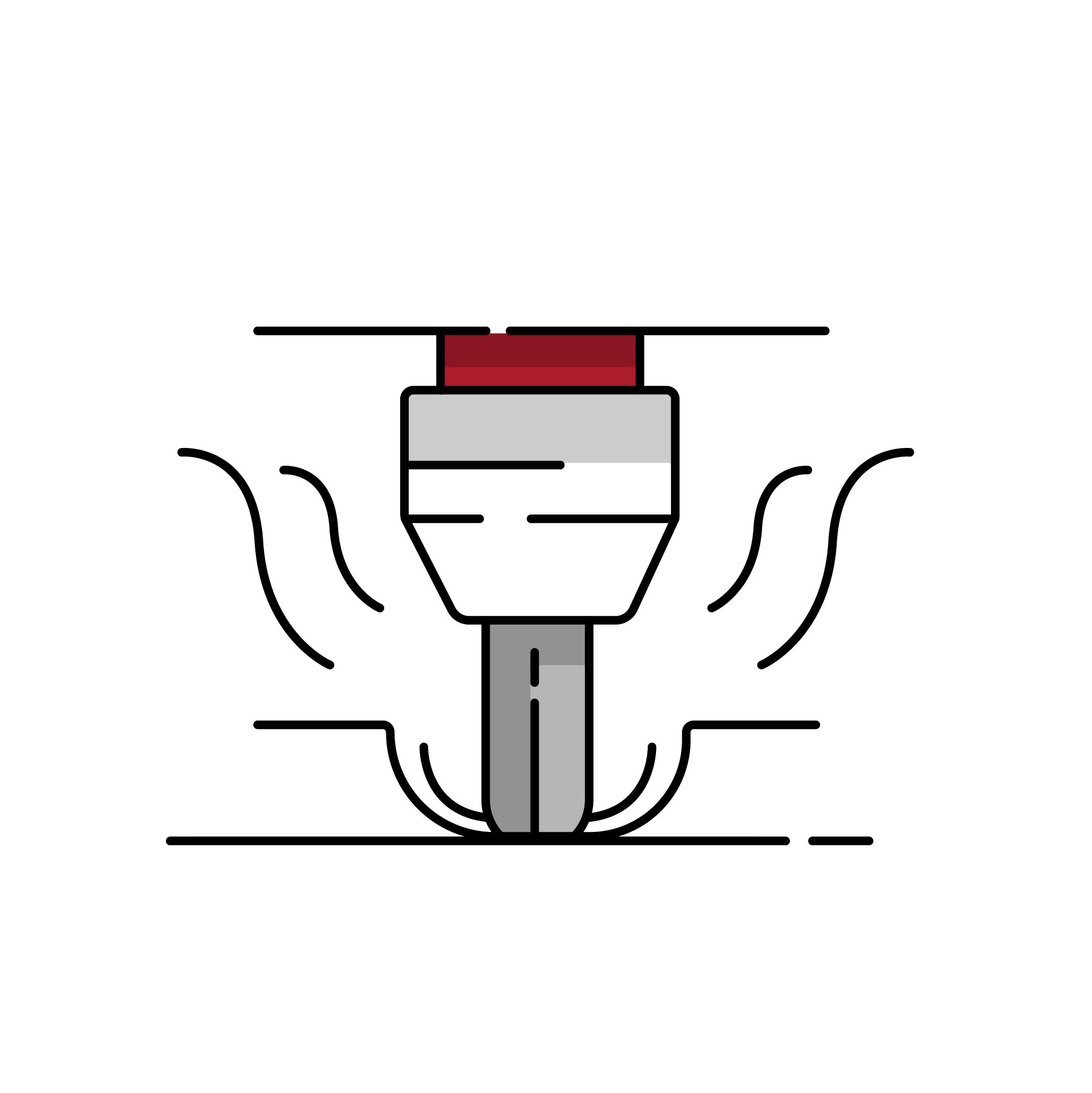
Machining
Whether you are turning, milling or drilling, get the information you need to complete your workpiece.
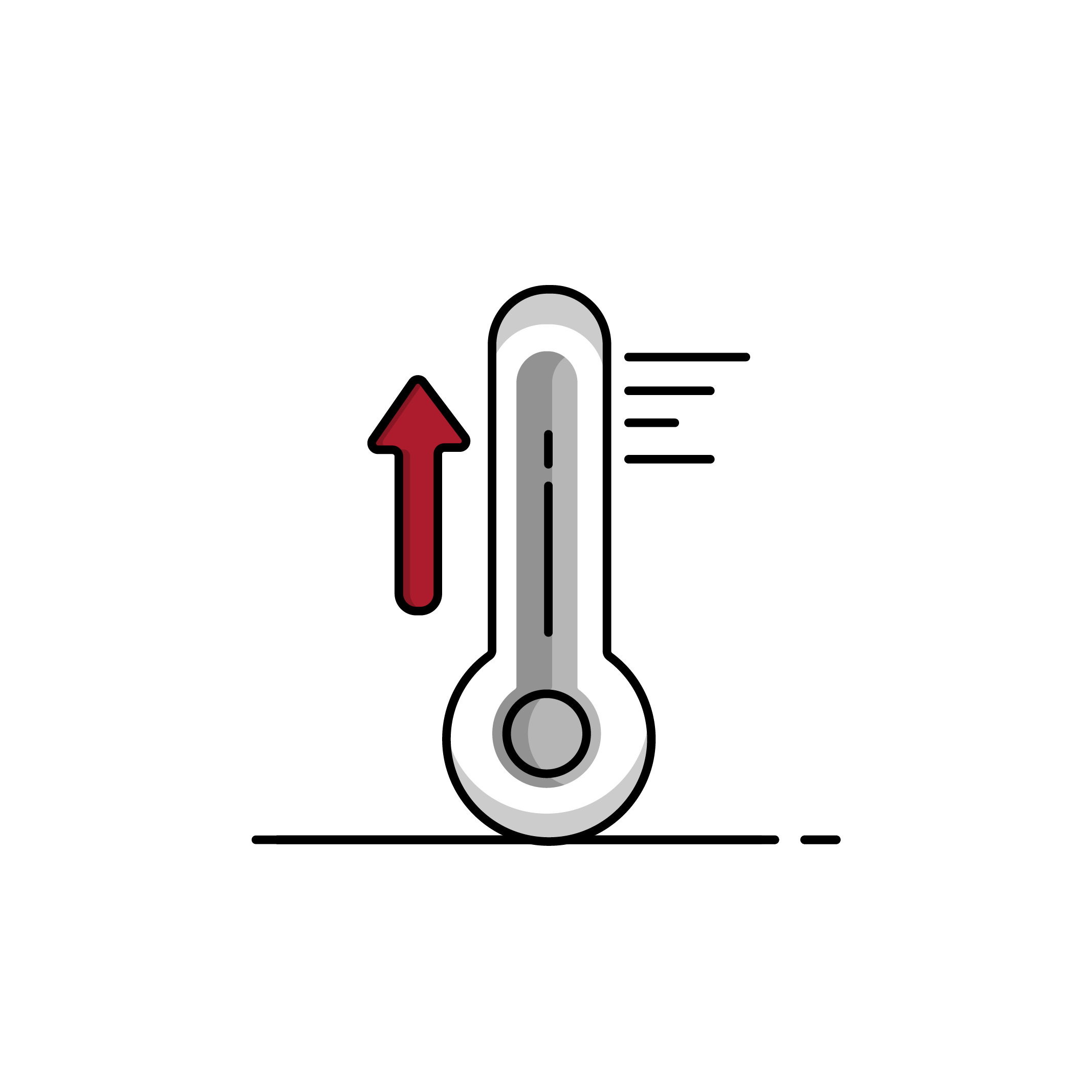
Thermal Expansion
Learn how stresses from unequal temperature distribution can cause failures.
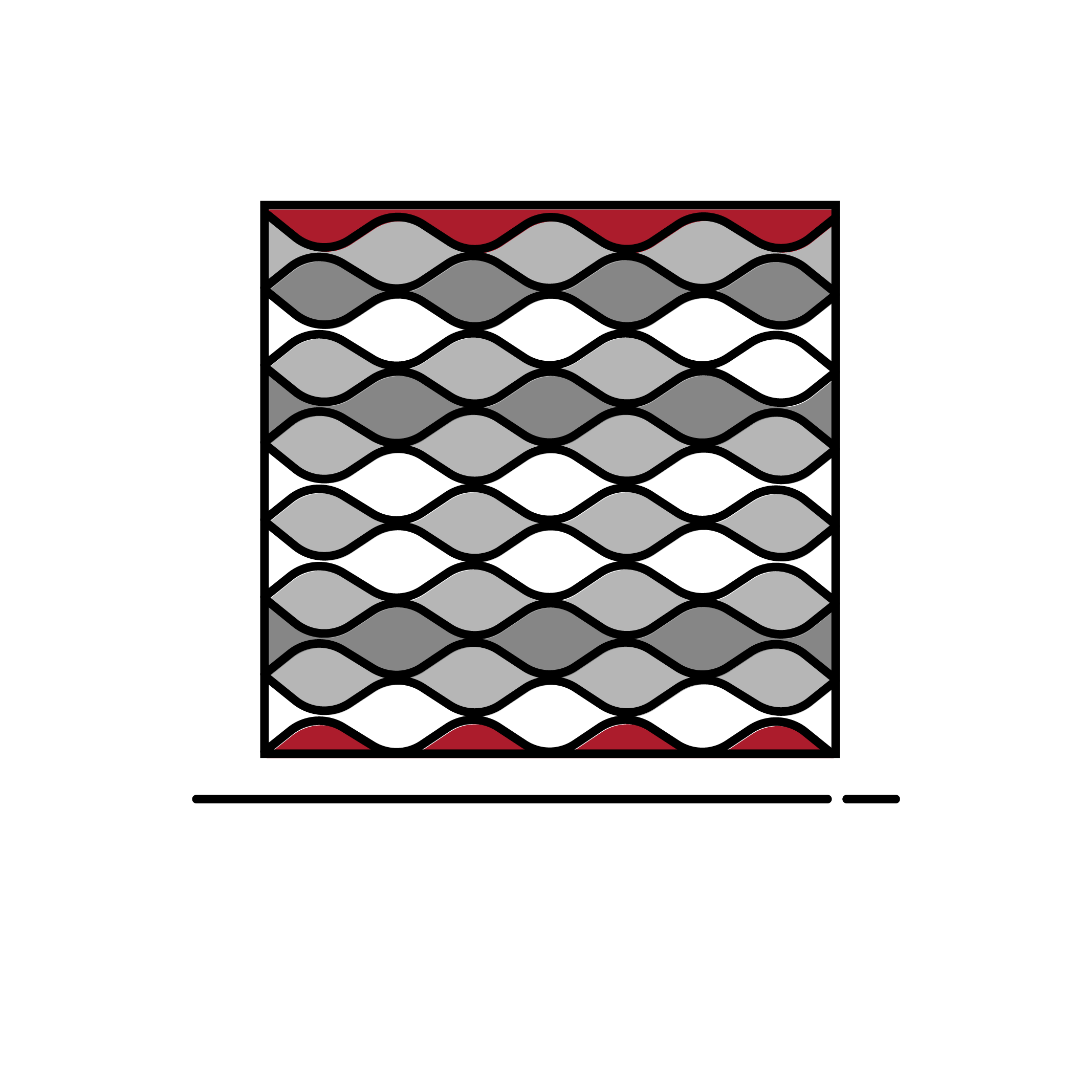
Cast vs Wrought
Guidelines for cast vs wrought material selection in high temperature applications.
Technical Resources
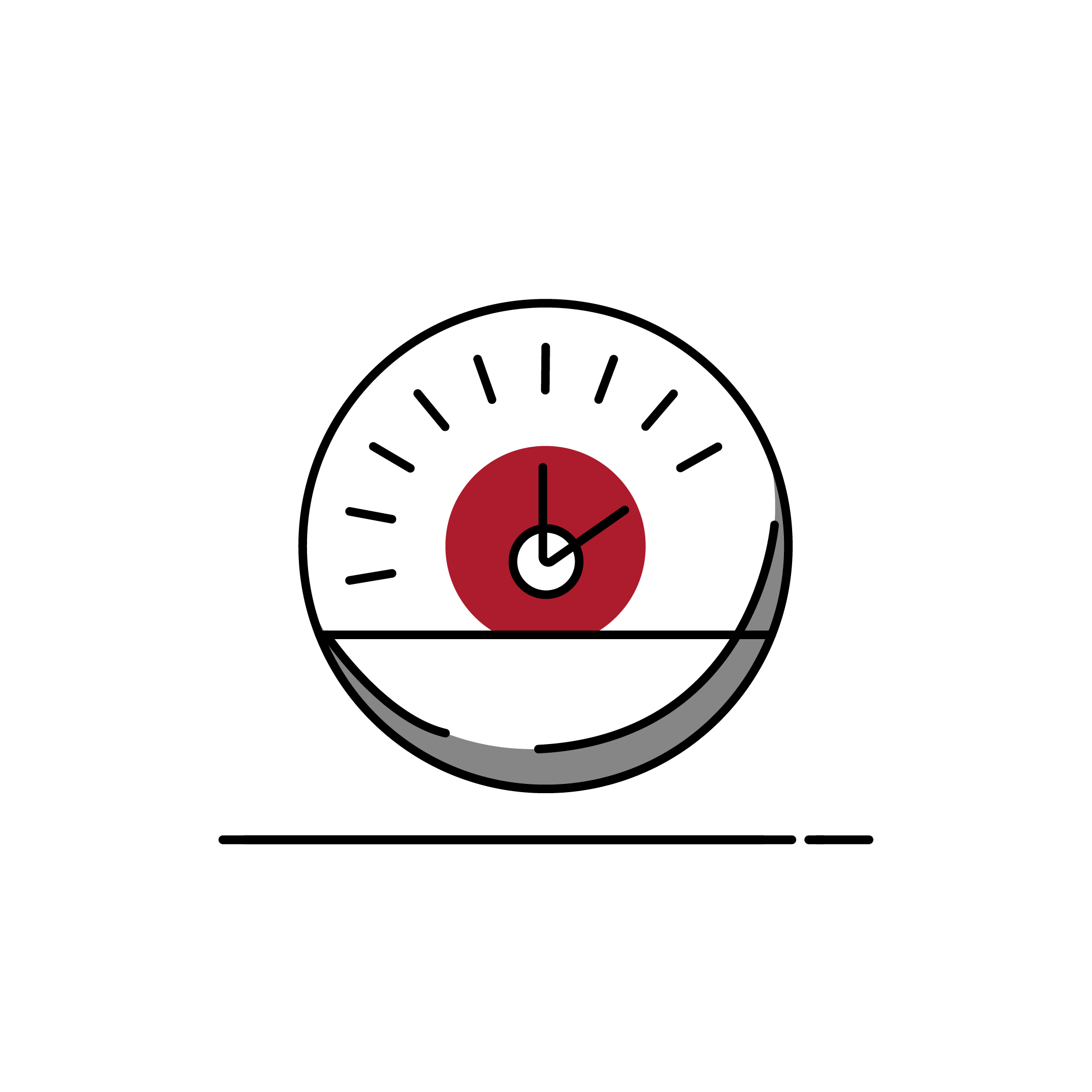
Performance Guide
An overview of our alloys' performance in many different environments.
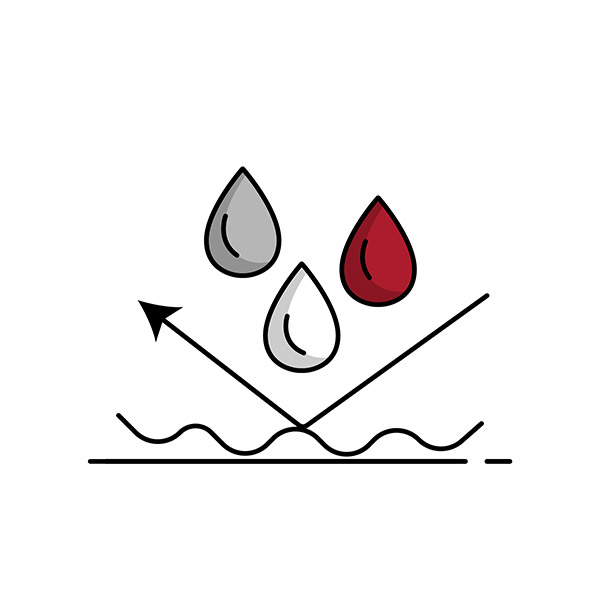
Environments
Find information to decide which alloy to use in high temperature and corrosive environments.
Frequently Asked RAMS Questions
Rolled Alloys’ materials are typically certified to ASTM, ASME, AMS, GE, and Pratt & Whitney specs, as well as others. For additional information about specifications, contact a Sales Representative.
In many instances they can. Please click on Chat or contact a Sales Representative for upgrading material specifications and mill certifications.
For a complete listing of our cutting tolerance capabilities, click here.
MIG (Metal Inert Gas) welding, also known as GMAW (Gas Metal Arc Weld), is always done with spooled wire, usually 0.035″ or 0.045″ rarely 0.062″. TIG (Tungsten Inert Gas) welding, also known as GTAW (Gas Tungsten Arc Weld), is usually done with 36″ straight lengths of bare wire. Automatic TIG machines may use spooled wire but 36″ lengths of wire are only used for TIG. Electrodes, commonly called “stick welding”, are typically 14″ lengths of wire, coated with a gray flux over all but the last 1-1/2 to 2″. For a full description of each click here.
For detailed information on alloy choices, visit our Technical Resource Center. For a downloadable Alloy Performance Guide pdf click here. You can also click on Chat or contact a Metallurgist at 1-800-521-0332.
Click here to view machinability guidelines.
Click here to view information on thermal expansion.
Click here to view strength table.